Round and Deformed Bar
RSM Rolling mill can produce standard construction steel bar (both round and deformed bar) from size 6 mm. to 52 mm. in diameter (grade: SR24, SD30, SD40 and SD50).
Steel Production Procedure
Steel bar rolling process starts from charging billet into re-heating furnace continuously, heating it up to 1050 c- 1100 c and discharging hot billet to the rolling mill train. Then rolls and reduces billet through rolling stand until it reaches the required size.
Normally, small bar needs to pass more rolling stand than large bar which results in a higher speed in production process.
Bar size with diameter of 20 mm. or more requires only the first eighteen stands to roll while the smaller size bar from 16 mm. or less needs to pass additional two to six stands more with a higher speed.
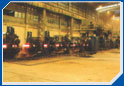 After reaching the required size, the finished large size bars will pass through low speed line, cut to length shear and discharge on to cooling bed by hydraulic apron. For the smaller size, the finished bar is cut to length by cutting to length shear on high speed line and discharging on to the cooling bed by double twin channels system.
After the bars temperature decreases naturally to approximately 80 íc - 150 íc from the cooling bed, the roller table exist side cooling bed will convey the bars direct to cold shear for commercial length cut (10 meters or 12 meters, or special length depend on customer's specification). All cut bars will be sent to finishing area for re-counting and bundling before sending to warehouse.
Wire Rod
RSM can produce standard wire rod from diameter of 5.5 mm. up to 19 mm. for low, medium, high carbon and special grade wire rod according to Thai Insdustrial Standards (TIS), Japanese Industrial Standards (JIS) and The American Society for Testing and Materials (ASTM).
Wire Rod Production Precedure
Wire Rod production has similar procedure as production of bar (with Diameter 20 mm. or more) It starts from re-heating billets to rolling pass 18th stands. After the 18th stand, bars will further reduce to required size through high speed finishing block (ten stands). For small size wire rod, the speed can be increased up to 120 meter/second. After finished rolling, the bars will pass directly to laying head or coil former, then drop on to the cooling conveyor which convey the coil to the coil collector, c-hook conveyor, coil compactor, tying machine and weight station for checking the coils weight before discharging to warehouse.
Quality Control
In order to fulfill RSM commitment to produce a superb quality of products, all products have to pass a strict quality control to achieve the specified industrial standards. There are two major quality control steps during production procedures.
Quality Control during production process
The objective of quality control during production process is to check the size, weight, and appearance of finished product by taking random samples of steel bar and wire rod every half an hour from rolling stand number six, twelve and finished product.
Quality Control by Quality Control Department (QC)
The Quality Control technicians not only look at physical appearance of finished product, but they also concern with mechanical properties and chemical composition, To check physical appearance, mechanical properties and chemical composition, the quality control technicians will take randomly samples of finished product at least three pieces from every lot. The mechanical properties testing will include tensile strength, yield strength testing and elongation while chemical composition test has to follow the Thai Industrial Standards (TIS).
Ratchasima Steel Products Company Limited :
269 Moo 1 (Km. 237) Mittraparb Road, Tambon Kok-kruad, Ampour Muang, Nakornratchasima Province, 30000
Tel. 0-4429-1888-99 Fax. 0-4439-5133, 0-4439-5126
|